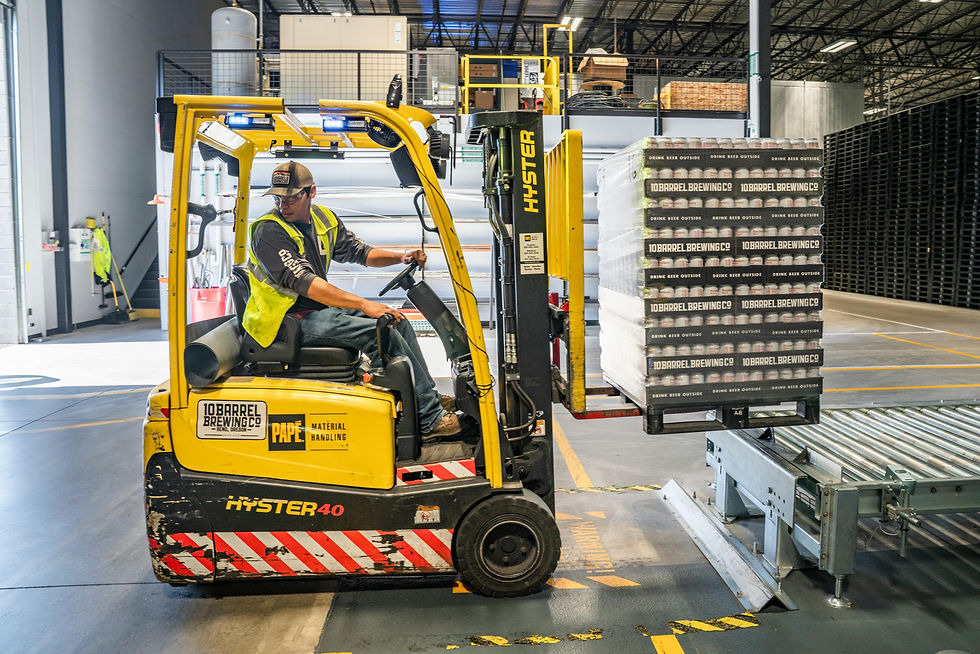
When it comes to freight shipping, mistakes can lead to costly delays, damaged goods, lost business, and customer dissatisfaction. Many of these issues can be prevented with proper planning, communication, and knowledge. Here are some of the most common freight shipping mistakes and how to avoid or solve them:
1. Incorrectly Classifying Freight
Problem: Freight classification determines shipping costs, and using the wrong classification can lead to unexpected charges. Many shippers use the wrong National Motor Freight Classification (NMFC) codes, leading to cost overruns.
Solution:
Double-check the freight classification and ensure it is accurate. Freight classification depends on several factors like weight, dimensions, density, value, and handling requirements.
Use tools like the National Motor Freight Traffic Association (NMFTA) Guide or consult your carrier or freight broker to confirm the proper classification.
Implement a system for consistently reviewing freight classifications to prevent future issues.
2. Poor Packaging
Problem: Shipping items that aren’t properly packaged can lead to damaged goods, delays, or even loss of the shipment. Packaging that isn’t strong enough for the shipment’s weight, size, or type can also result in additional fees.
Solution:
Ensure that all items are packaged securely, using appropriate materials (such as bubble wrap, foam, or corrugated boxes) that can withstand rough handling.
Follow the Carrier’s Packaging Guidelines for each shipping mode (e.g., truck, rail, or ocean).
Consider investing in custom packaging if your products have unique shapes or fragile components.
Take photographs of the packaged goods before shipping to document their condition.
3. Not Using the Right Shipping Mode
Problem: Choosing the wrong shipping mode (e.g., truck vs. rail vs. air) can result in higher costs or delays. For example, using air freight for large shipments when truck or rail would be more cost-effective.
Solution:
Evaluate the size, urgency, and destination of your shipment before choosing the shipping method.
Use intermodal transportation when possible to save on costs while maintaining efficiency. For example, use a combination of rail for long distances and truck for last-mile delivery.
Work with a freight broker to help determine the most cost-effective mode of transport based on your needs.
4. Neglecting to Account for Customs Requirements (For International Shipping)
Problem: Shipping internationally involves complex customs documentation and clearance processes. Failing to provide the correct documents or incorrectly completing them can lead to delays, fines, and goods being held at customs.
Solution:
Research the specific customs requirements for the destination country and ensure that all paperwork (such as commercial invoices, packing lists, and certificates of origin) is accurate and complete.
Work with a customs broker to assist with compliance, or ensure your freight forwarder handles customs clearance.
Always anticipate potential delays at customs, especially during peak seasons.
5. Not Double-Checking the Delivery Address
Problem: Sending shipments to incorrect or incomplete addresses can lead to delays, return shipments, or lost goods.
Solution:
Always verify the recipient’s address before shipping, including the zip code, contact details, and any special delivery instructions.
Use address verification tools or consult the recipient to confirm shipping details, especially for international shipments where addresses can vary greatly.
For larger shipments, include the specific delivery point (e.g., warehouse, loading dock) to prevent confusion.
6. Underestimating Shipment Size and Weight
Problem: Incorrectly estimating the weight or dimensions of the shipment can lead to unexpected costs or issues during transport. Overestimating or underestimating the size of the shipment can result in additional fees or a delayed shipment.
Solution:
Weigh and measure your shipment accurately before sending it.
Always include the exact dimensions (length, width, height) and weight of the cargo to avoid discrepancies when the carrier assesses it.
If unsure, work with a freight broker to help you accurately determine size and weight.
7. Failing to Plan for Delivery Delays
Problem: Freight shipments can be delayed due to factors such as weather, equipment malfunctions, or customs holdups. Not accounting for potential delays can disrupt your operations and cause customer dissatisfaction.
Solution:
Plan for contingencies by setting realistic expectations for delivery times, especially during busy seasons (e.g., holidays).
Use tracking software or work with your carrier to monitor shipments in real time.
Communicate proactively with customers and partners about potential delays, and offer alternatives (e.g., expedited shipping) if necessary.
8. Inaccurate Billing and Charges
Problem: Hidden charges, unexpected fees, or mistakes in the billing process can result in much higher costs than anticipated.
Solution:
Always request and review a quote or estimate before confirming the shipment, including all potential fees such as fuel surcharges, accessorial charges, and loading/unloading fees.
Verify that the bill of lading (BOL) and invoice match the agreed-upon terms.
Regularly review your shipping invoices for discrepancies, and work with your freight provider to resolve any issues.
9. Not Taking Advantage of Freight Insurance
Problem: Not purchasing freight insurance or relying solely on carrier liability can leave you exposed in the event of lost, damaged, or stolen goods.
Solution:
Consider purchasing freight insurance that covers the full value of your goods, especially if shipping high-value or fragile items.
Be aware of the carrier’s limited liability and understand its coverage limits (e.g., $0.10 per pound).
If your shipment is particularly valuable, research and obtain additional coverage tailored to your needs.
10. Failure to Communicate with Carriers or Freight Providers
Problem: Poor communication with carriers or freight brokers can lead to misunderstandings, missed deadlines, or incorrect routing.
Solution:
Maintain clear communication with your carriers, freight forwarders, and anyone involved in the shipping process.
Regularly confirm shipment details (pickup, route, destination, special requirements) in advance.
Keep contact information handy for emergencies or urgent updates.
Use a transportation management system (TMS) to streamline communication and tracking across all parties.
11. Not Reviewing Shipping Contracts Regularly
Problem: Shipping contracts and rates can change over time, and failing to review them regularly can lead to overpaying for services or not taking advantage of updated terms.
Solution:
Regularly review your shipping contracts to ensure you're still getting the best rates and services.
Negotiate with carriers for better rates or explore alternative shipping partners if costs are rising.
Keep an eye on market trends and adjust your strategies to stay competitive.
Conclusion:
Avoiding these common freight shipping mistakes requires attention to detail, proactive planning, and good communication with carriers and partners. By taking the time to properly classify your freight, ensure packaging and documentation are correct, and review your shipping strategies, you can prevent many costly issues before they arise and keep your supply chain running smoothly. If you're unsure about any aspect of your shipping process, consider working with a trusted freight broker or logistics expert who can guide you through the complexities and help you optimize your shipping operations.
Comments